Regular maintenance is often overlooked, yet it’s vital for equipment longevity, especially for those relying on commercial septic tank pumping solutions.
This article will cover essential maintenance tasks, best practices for extending equipment life, and the consequences of neglecting upkeep.
By understanding these aspects, readers can ensure their systems run smoothly and efficiently, ultimately saving money and avoiding costly repairs. If you want to avoid disruptions and learn from the experts at Smart Septic Pros, keep reading. For more information, feel free to contact us or learn about our experts.
Why Regular Maintenance is Key to Equipment Longevity
Understanding the Importance of Regular Maintenance for Equipment Longevity
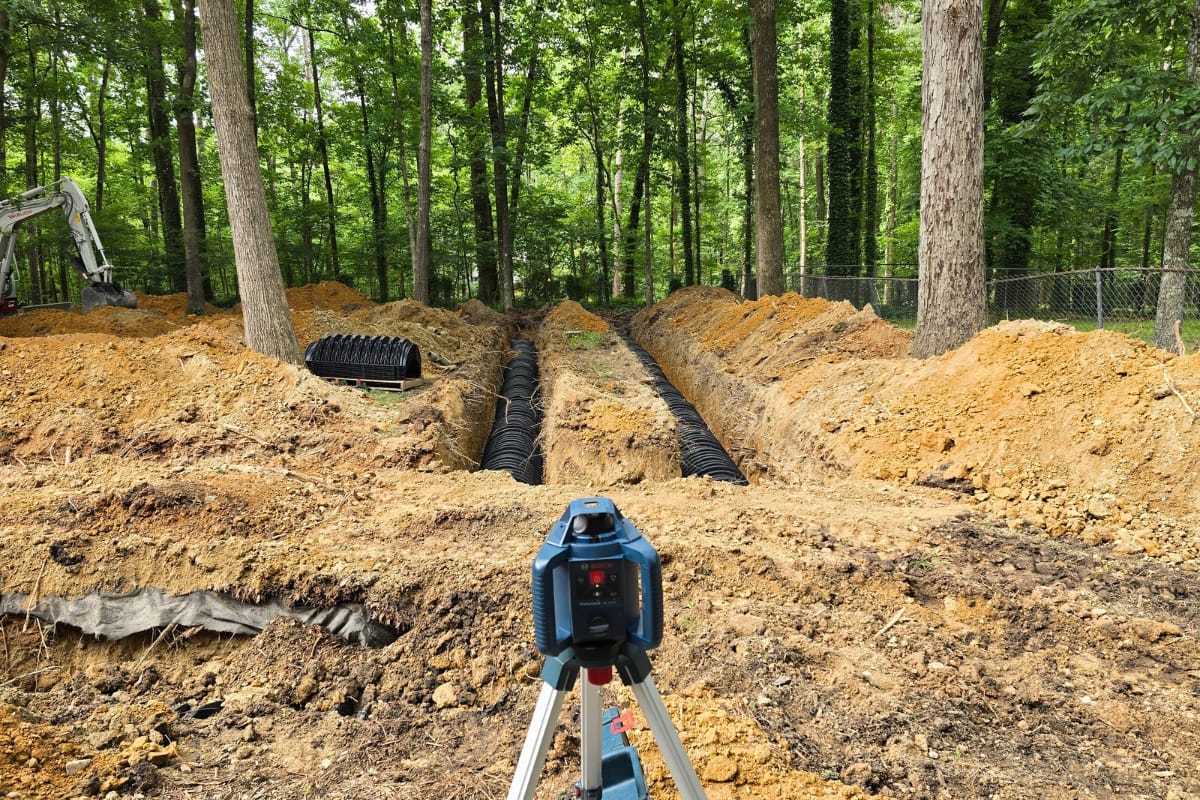
Regular maintenance by Smart Septic Pros, septic tank installers, plays a crucial role in enhancing the lifespan of equipment, especially in the context of septic systems.
Neglecting maintenance can lead to significant durability issues and unforeseen septic emergencies.
Additionally, professional septic tank pumping and commercial septic tank pumping, along with proper septic tank pumping frequency, is key for avoiding costly repairs, and implementing septic maintenance tips ensures safety and compliance.
Role of Maintenance in Enhancing Equipment Lifespan
Regular maintenance is essential for extending the lifespan of machinery in manufacturing settings. Keeping machines in good working order involves timely calibration, which ensures they operate at peak efficiency. Utilizing data and analytics can also help identify maintenance patterns and potential issues before they lead to costly repairs.
Moreover, proactive maintenance fosters a safer work environment. By regularly inspecting equipment and addressing wear and tear, manufacturers can prevent unexpected breakdowns that could disrupt production.
This approach not only supports the longevity of the machines but also enhances overall productivity, allowing businesses to meet demand without unnecessary downtime.
Impact of Neglecting Maintenance on Equipment Durability
Neglecting maintenance can severely impact the durability of equipment, leading to unexpected breakdowns and reduced productivity. When businesses bypass regular septic tank pumping frequency, they might face increased repair costs and longer downtimes, hampering their overall efficiency.
Predictive analytics play a vital role here, as they can highlight maintenance needs before they escalate into critical issues, allowing companies to stay ahead of potential problems and keep their assets running smoothly.
Without a solid maintenance plan, the performance of machinery can drop significantly over time. This decline often leads to unplanned outages that disrupt workflow and negatively affect productivity.
By incorporating predictive maintenance strategies such as commercial septic tank pumping and septic tank pumping frequency, and septic tank installers, companies can maximize the longevity of their equipment while ensuring that operations remain uninterrupted, ultimately safeguarding their investments and maintaining a competitive edge.
Long-Term Cost Benefits of Regular Maintenance
Investing in a computerized maintenance management system (CMMS) or inventory management software can yield significant long-term cost benefits for businesses.
These tools help track maintenance schedules, ensuring that necessary upkeep such as commercial septic tank pumping frequency is performed consistently. By using a simple checklist within the software, companies can prevent overlooked tasks, reduce repair costs, and prolong the lifespan of their equipment.
The internet offers a wealth of resources to streamline maintenance strategies, allowing businesses to monitor equipment health in real time. When companies prioritize regular maintenance, including septic tank pumping frequency, they often notice fewer major repairs and minimize downtime, leading to improved productivity.
This proactive approach not only conserves funds over time but also enhances overall operational efficiency, making it a smart choice for any organization.
Importance of Safety and Compliance in Equipment Maintenance
When it comes to equipment maintenance, safety, and compliance shouldn’t be afterthoughts. Regular inspections by septic tank installers help identify issues like leaks or excessive heat that could compromise safety.
By keeping up with condition monitoring and commercial septic tank pumping frequency and ensuring compliance with regulations, businesses protect their assets and create a safer work environment for everyone. For more information, contact us and learn about our experts from smart septic pros.
Effective asset management involves not just maintaining equipment, but also safeguarding employees against potential hazards. Routine check-ups by septic tank installers and septic tank pumping frequeny can reveal problems before they escalate, helping to avoid accidents and costly downtime.
Additionally, commercial septic tank pumping ensures that large-scale operations maintain optimal performance. By prioritizing safety within maintenance routines, companies enhance operational efficiency and secure their investments for the long term.
Regular maintenance keeps equipment running well and extends its life. Next, we will look at the essential tasks that should not be overlooked.
Essential Maintenance Tasks for Equipment
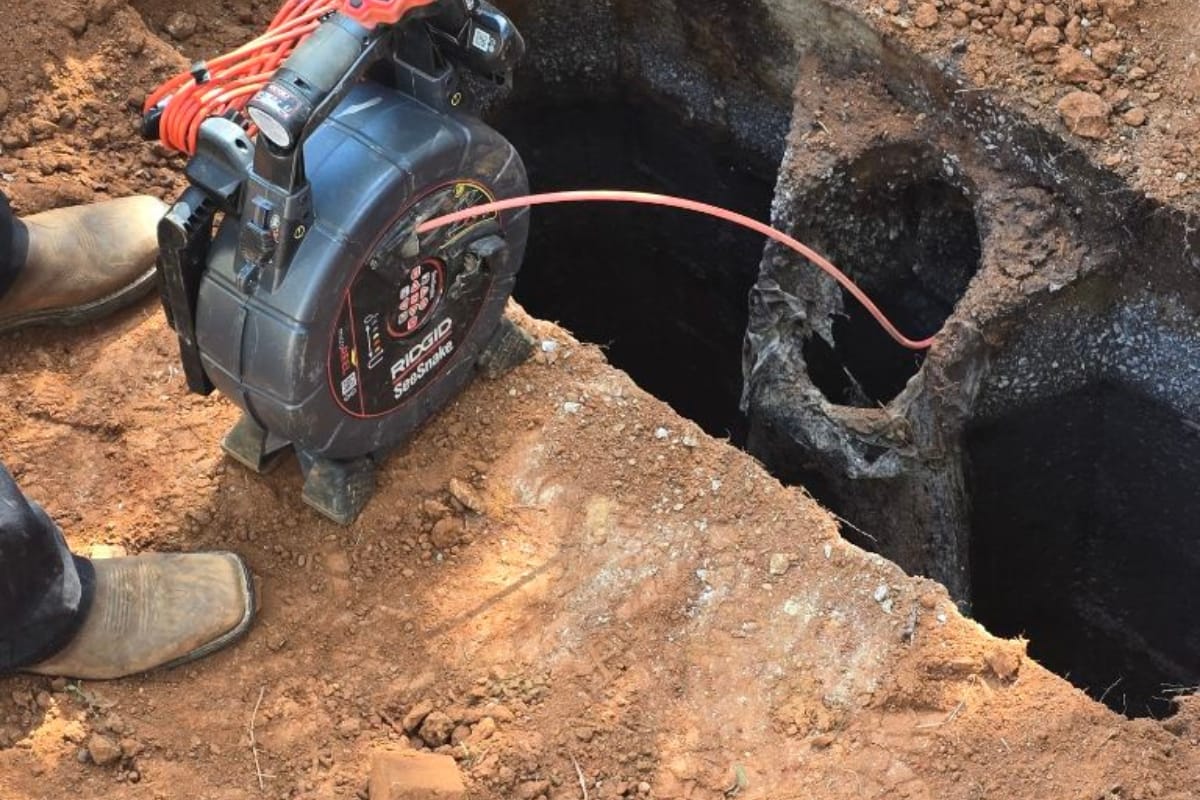
Regular inspection and assessment procedures are vital for identifying potential failures before they occur. The importance lies in consistent cleaning and lubrication, ensuring equipment runs smoothly.
Scheduling repairs proactively prevents unexpected breakdowns. Documenting maintenance activities, including septic tank pumping frequency, provides a clear history while utilizing technology, such as enterprise asset management tools, streamlines task management and enhances efficiency. Each of these aspects greatly contributes to extending equipment longevity.
Regular Inspection and Assessment Procedures
Regular inspection and assessment procedures are vital for keeping machinery in top condition and addressing wear and tear before they turn into bigger issues.
These inspections help identify any signs of wear, such as unusual sounds or heat, which can lead to costly downtime if neglected. By proactively addressing these concerns, companies can effectively mitigate risks and ensure their equipment remains compliant with regulatory standards.
For specialized services, contact us to learn about our experts and our commercial septic tank pumping offerings provided by smart septic pros and our experienced septic tank installers. Additionally, understanding the septic tank pumping frequency can help in planning maintenance schedules effectively.
Conducting routine assessments allows businesses to stay ahead of potential problems and maintain efficient operations. For instance, operators can monitor fluid levels and replace worn parts, which prevents unexpected breakdowns and extends equipment life.
Tracking septic tank pumping frequency not only enhances productivity but also provides peace of mind knowing that safety measures and compliance requirements are being met.
Maintenance Task | Description | Benefits |
---|---|---|
Regular Inspections | Routine checks on equipment for signs of wear. | Reduces downtime and prevents major failures. |
Fluid Checks | Monitoring oil, coolant, and other fluid levels. | Prevents overheating and maintains performance. |
Part Replacement | Replacing worn or damaged components promptly. | Extends equipment lifespan and ensures uptime. |
Documentation | Keeping a log of all maintenance activities. | Ensures regulatory compliance and provides a history of care. |
Importance of Cleaning and Lubrication
Maintaining cleanliness and proper lubrication in heavy equipment is essential for ensuring long-term efficiency and health. Keeping machinery free from dirt and grime not only supports hygiene but also prevents wear and tear that can lead to significant repair costs.
Regular cleaning routines, septic tank installers, and septic tank pumping frequency help operators identify potential issues early, ensuring that equipment remains in peak condition and within the allocated budget.
Lubrication is another critical aspect of maintenance, as it reduces friction and heat between moving parts, promoting smooth operation. By attending to lubrication and septic tank pumping frequency schedules, companies enhance equipment performance and prolong lifespan.
Ultimately, focusing on these maintenance tasks not only contributes to productivity but also fosters a safer working environment by reducing the risk of equipment failure.
Scheduling Repairs Before Failures Occur
Scheduling repairs before failures occur is a crucial component of a robust maintenance strategy. By conducting regular inspections and monitoring equipment for signs of issues like abnormal vibrations or oil leaks, companies can catch potential problems early.
Utilizing automation tools with built-in sensors can streamline this process, including commercial septic tank pumping, providing alerts when equipment requires attention, thus preventing unexpected breakdowns and ensuring septic tank pumping frequeny, occupational safety, and health standards are met.
Proactive scheduling helps organizations save time and money in the long run. For example, replacing worn parts and addressing minor issues before they escalate into major repairs can significantly minimize downtime.
By taking steps to maintain equipment health, such as commercial septic tank pumping and septic tank pumping frequeny, businesses can optimize performance and extend the lifespan of their machinery.
Maintenance Task | Description | Benefits |
---|---|---|
Regular Inspections | Routine checks on equipment for signs of wear. | Reduces downtime and prevents major failures. |
Fluid Checks | Monitoring oil, coolant, and other fluid levels. | Prevents overheating and maintains performance. |
Part Replacement | Replacing worn or damaged components promptly. | Extends equipment lifespan and ensures uptime. |
Documentation | Keeping a log of all maintenance activities. | Ensures regulatory compliance and provides a history of care. |
Documentation of Maintenance Activities
Maintaining thorough documentation of maintenance activities, such as septic tank pumping frequency, is vital for preventing emergencies and ensuring equipment accessibility across various industries like health care, construction, and septic tank installers.
Detailed records can reveal patterns that highlight when issues may arise, allowing businesses to take proactive measures before problems escalate into costly breakdowns.
For instance, in health care settings, this is particularly crucial to avoid contamination risks and maintain a safe environment for patients and staff.
Additionally, clear documentation supports compliance with regulations, ensuring companies avoid penalties and maintain operational efficiency. Tracking maintenance activities not only streamlines the upkeep process but also provides a historical reference that can be invaluable during audits or inspections.
A well-organized maintenance log serves as a roadmap for equipment health, helping organizations plan resources effectively and reducing the likelihood of unexpected equipment failures.
Utilizing Technology in Maintenance Task Management
Utilizing technology in maintenance task management can significantly boost an organization’s efficiency and resource use. For instance, software that tracks maintenance schedules ensures timely replacements, like changing air filters, which not only improves air quality but also supports equipment longevity.
By having access to real-time information from septic tank installers, organizations can prioritize maintenance tasks effectively, thus conserving energy and minimizing costs associated with equipment failures.
Adopting digital solutions enables companies to monitor their systems more closely, allowing for quicker detection of issues before they escalate.
This proactive approach not only enhances the performance of septic tank installers but also fosters a culture of continuous improvement within the organization.
Integrating septic tank pumping frequency and commercial septic tank pumping into maintenance activities simplifies processes, ensuring that equipment remains operational and extends its useful life.
Every touch and tweak adds life to machinery. The path to lasting performance lies in understanding the best practices for care.
Best Practices for Achieving Equipment Longevity
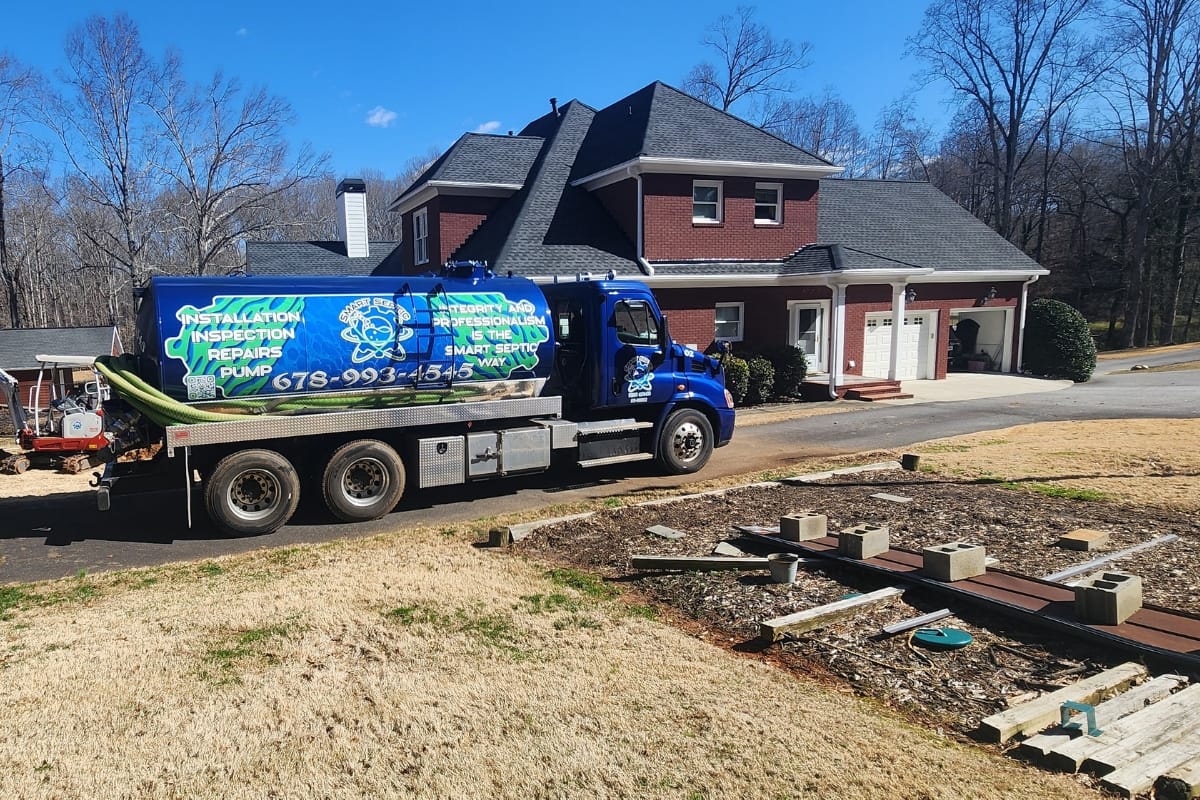
Developing a comprehensive maintenance plan is vital for maximizing equipment longevity. Training staff on proper procedures ensures knowledgeable handling, while implementing condition-based monitoring, such as septic tank pumping frequency, can catch issues early.
Establishing emergency maintenance protocols prepares teams for unforeseen breakdowns, including commercial septic tank pumping, and auditing practices support continuous improvement.
Each of these best practices highlights the ongoing investment in equipment health, essential for keeping engines running smoothly and plumbing systems efficient.
Developing a Comprehensive Maintenance Plan
Creating a comprehensive maintenance plan is essential for ensuring the long-term performance of equipment. This plan should outline regular checks on critical components, such as septic tank pumping frequency, septic tank installers, hydraulic fluid levels, and pressure gauges, as well as the use of personal protective equipment to guarantee worker safety during maintenance tasks.
Additionally, utilizing services like commercial septic tank pumping can enhance the effectiveness of the maintenance plan.
By incorporating strategies like condition-based monitoring with the Internet of Things (IoT), businesses can detect potential issues early, which leads to a strong return on investment by reducing downtime and unexpected repairs.
Moreover, training staff on the importance of adhering to the maintenance schedule, including septic tank pumping frequency and commercial septic tank pumping, is vital. When employees understand the significance of each step in the plan, they are more likely to follow through.
This approach creates a culture where equipment health is prioritized by septic tank installers, ultimately preventing costly breakdowns and enhancing overall productivity. contact us.
- Develop a structured maintenance plan for equipment.
- Include regular checks on hydraulic fluid and pressure levels.
- Incorporate the use of personal protective equipment for safety.
- Utilize the Internet of Things to monitor equipment conditions.
- Train staff to ensure adherence to maintenance schedules.
Training Staff on Equipment Maintenance Procedures
Training staff on equipment maintenance procedures is essential for ensuring safety and prolonging the life of machinery. Workers who understand the importance of regular inspections can identify issues like dust buildup or mechanical wear before they escalate into problems.
Monitoring septic tank pumping frequency is part of these inspections. For instance, teaching operators to recognize abnormal sounds can lead to quicker interventions, preventing costly downtime and ensuring that equipment runs smoothly. Additionally, for specialized tasks such as commercial septic tank pumping, it’s advisable to contact experts to ensure proper maintenance.
Moreover, proper training fosters awareness of access control and surveillance measures that protect equipment from unauthorized use or contamination.
When employees know how to properly maintain and monitor equipment, it reduces the chances of organisms or harmful substances affecting operational integrity.
This proactive approach not only enhances safety but also cultivates a shared responsibility among staff for maintaining equipment health, ultimately leading to improved productivity and reduced repair costs.
Implementing Condition-Based Monitoring
Implementing condition-based monitoring is a wise move for maintaining equipment longevity, especially in environments like commercial kitchens that rely heavily on hydraulics and pumps.
By using sensors to track the health of different components, businesses can identify when parts need attention before they lead to major failures. This proactive approach not only streamlines workflow but also significantly reduces unexpected expenses associated with downtime and repairs.
Establishing Emergency Maintenance Protocols
Establishing emergency maintenance protocols is crucial for effective equipment management. Organizations should train their staff to recognize the frequency of maintenance needs and understand when immediate attention is required.
This preparedness helps minimize disruptions and extends the lifespan of machinery like vehicles, ensuring they remain operational even in unforeseen circumstances.
By creating a clear plan that outlines steps to take during emergency situations, companies can prevent equipment failures from escalating into costly repairs.
Scheduling regular drills and reviews of these protocols ensures that everyone knows their role and can respond swiftly—reducing downtime and keeping projects on track. Such proactive measures not only improve operational efficiency but also foster a culture of safety and accountability within the team:
Emergency Protocol Step | Description | Expected Outcome |
---|---|---|
Identify Critical Equipment | List machines that require immediate attention. | Focus resources efficiently. |
Training Sessions | Regular workshops to discuss protocols. | Better preparedness and response times. |
Maintenance Schedule | Create a detailed maintenance frequency plan. | Reduce unexpected equipment failures. |
Emergency Contacts | List contacts for service and parts suppliers. | Quick recovery in emergencies. |
Auditing Maintenance Practices for Continuous Improvement
Regularly auditing maintenance practices for heavy equipment is a key strategy for continuous improvement in equipment longevity. These audits should focus on assessing adherence to maintenance schedules and identifying areas for improvement in equipment maintenance protocols.
For instance, if a specific piece of machinery consistently shows signs of wear early, this may indicate that the existing maintenance tips need adjustment to better suit the equipment‘s needs.
Conducting these audits not only helps maintain proper function but also empowers businesses to implement best practices that enhance operational efficiency.
By closely monitoring equipment performance and maintenance records, organizations can pinpoint recurring issues and take action to prevent them. This proactive mindset can ultimately lead to a more effective maintenance strategy, ensuring equipment remains functional and reliable for years to come.
Maintaining equipment well leads to a smooth, efficient operation. Neglecting it, on the other hand, can turn a small issue into a costly problem that lingers far too long.
The Consequences of Poor Maintenance on Equipment Longevity
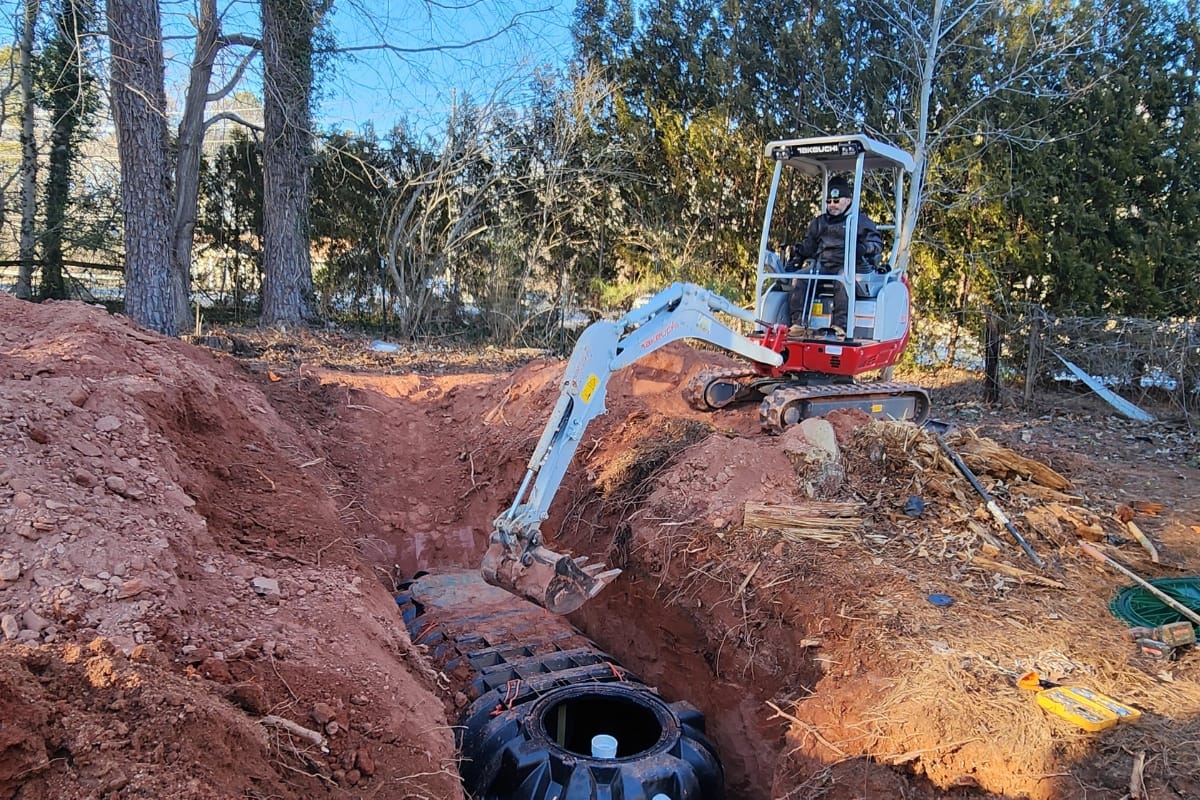
Neglecting maintenance leads to an increased risk of equipment failure, which can result in higher replacement costs over time. Operational efficiency often diminishes as machines struggle to perform optimally, while compromised safety standards can pose serious risks.
Each of these aspects highlights the necessity of using preventive maintenance software to ensure a proper lifecycle and timely backups, ultimately saving costs and maintaining a productive workplace.
Increased Risk of Equipment Failure
Neglecting routine maintenance significantly increases the risk of equipment failure, impacting overall productivity. For instance, a conveyor belt that hasn’t been regularly inspected may develop issues that lead to costly downtimes or even complete breakdowns.
Establishing a culture of accountability within teams can encourage proactive maintenance practices, helping to prevent these issues before they arise.
A robust maintenance strategy is essential to ensure equipment longevity. Businesses can leverage inventory management systems to track maintenance needs and schedules effectively.
By integrating regular checks into the workflow, organizations not only reduce the risk of unexpected equipment failure but also foster a safer and more efficient work environment:
- Establish a culture of accountability among staff.
- Implement a proactive maintenance strategy.
- Utilize inventory management systems to track equipment health.
Higher Replacement Costs Over Time
Ignoring regular maintenance can lead to significantly higher replacement costs for equipment over time. For example, a truck that experiences engine failure due to lack of oil changes may require a complete engine replacement, a costly ordeal that could have been prevented with routine upkeep.
This is particularly relevant in facilities where resource allocation is limited; organizations that fail to invest in consistent maintenance are likely to face emergency replacements that disrupt operations and increase overall expenses.
Adopting modern practices like machine learning can help predict when maintenance is needed, reducing the risk of equipment failure in various systems. In a plant environment, monitoring data trends can identify wear and tear patterns, allowing companies to address issues before they escalate.
By implementing these proactive strategies, organizations can avoid sudden costs associated with equipment replacement, leading to better financial management and more efficient resource utilization:
Impact of Poor Maintenance | Consequences | Cost Implications |
---|---|---|
Truck Engine Failure | Complete engine replacement needed | High replacement costs |
Unscheduled Downtime | Disruptions in production | Loss of revenue |
Resource Allocation Issues | Emergency repairs required | Increased expenses |
Outdated Systems | Higher operational inefficiency | Long-term loss in profits |
Reduced Operational Efficiency
Neglecting regular maintenance can drastically reduce operational efficiency in various systems, including air conditioning units. When equipment becomes cluttered with debris or experiences corrosion, it struggles to operate effectively, leading to an increased mean time between failures.
Regular inspections, on the other hand, help to catch these issues early, ensuring that the infrastructure remains efficient and reducing the likelihood of costly breakdowns.
With poor maintenance practices, machines often operate under duress, which can be particularly evident in HVAC systems. For instance, when filters are not replaced regularly, airflow decreases, forcing the system to work harder and consume more energy.
This extra strain not only shortens the lifespan of the equipment but also drives up energy costs, ultimately affecting overall productivity and operational effectiveness.
Compromised Safety Standards
Compromised safety standards often arise from neglecting regular maintenance, creating risky environments in workplaces that rely on heavy machinery, servers, or utility systems.
For example, worn-out components can increase friction, resulting in dangerous overheating, which may lead to equipment failures and safety hazards. Implementing correct maintenance practices and continually learning about the best safety measures is essential to ensure that machinery operates without issues.
In industries where equipment directly impacts safety, such as manufacturing or utilities, neglect can lead to serious accidents. A proactive maintenance approach can help detect signs of wear and tear early, minimizing the risk of malfunctions.
Organizations that prioritize maintenance not only improve their operational efficiency but also cultivate a safer workplace for all employees:
- Safety improves with regular inspections.
- Reducing friction in machinery enhances performance.
- Corrective maintenance addresses issues before they escalate.
- Continuous learning fosters safer workplace practices.
The signs of neglect are clear, but the path to better care is wide open. Up next, common questions about maintenance will shed light on how to secure the lifespan of your equipment.
FAQs on Regular Maintenance and Equipment Longevity
This section addresses key questions about maintaining equipment, focusing on critical topics for factories and mining operations.
Readers will learn how often equipment should be serviced, recognize common signs that indicate maintenance is necessary, and explore whether proper upkeep can ensure gear longevity and life expectancy.
Additionally, resources for effective maintenance planning will be discussed, emphasizing sustainability integral to equipment management.
How Often Should Equipment Be Maintained?
Determining how often equipment should be maintained depends on several factors, including usage rates and manufacturer recommendations. For optimal performance, creating a preventive maintenance plan is essential.
This plan helps organizations schedule regular check-ups and inventory management to ensure that all necessary parts are available. Technicians can then perform troubleshooting tasks in a timely manner, preventing minor issues from escalating into significant problems.
In industries where equipment operates continuously, maintenance might need to occur as frequently as weekly or monthly.
Utilizing team software can streamline the tracking of maintenance schedules, ensuring that no task is overlooked. By staying proactive and adhering to a structured maintenance routine, organizations can enhance equipment reliability, ultimately leading to increased productivity and fewer unexpected breakdowns.
What Are Common Signs That Maintenance Is Needed?
Recognizing the signs that maintenance is needed can directly impact equipment longevity and operational efficiency. Common indicators include unusual sounds or vibrations that weren’t present before, which often suggest that something is amiss within the machinery.
Additionally, visible leaks or warning lights on equipment dashboards are clear signals for maintenance intervention, highlighting the need for immediate attention to avoid further damage.
Another sign to watch for is a decrease in performance, such as slower operation or increased energy consumption. Implementing a maintenance management system can help streamline the identification of these issues by providing regular updates and alerts for when action is required.
By using maintenance management software effectively, organizations can ensure consistent asset maintenance and make timely adjustments to keep operations running smoothly:
- Unusual sounds or vibrations
- Visible leaks or warning lights
- Decreased performance or energy efficiency
Can Equipment Longevity Be Guaranteed With Proper Maintenance?
While no one can guarantee the absolute longevity of equipment, adhering to a well-structured maintenance program significantly enhances its lifespan. Implementing a comprehensive preventive maintenance program, paired with maintenance software, allows businesses to track tasks effectively and ensures timely interventions.
By scheduling preventive maintenance routinely, companies can address issues before they turn into bigger problems, ultimately leading to better reliability and operation.
Consistent practices like routine inspections and timely repairs will lead to optimal performance and fewer costly breakdowns. Investing in a robust maintenance program not only safeguards equipment but also contributes to the overall efficiency of operations.
Understanding the importance of these strategies is essential for any organization aiming to prolong its equipment‘s life and maximize returns on investment.
- Implement a comprehensive preventive maintenance program.
- Utilize maintenance software for tracking and scheduling.
- Conduct routine inspections and timely repairs.
- Focus on consistent practices for optimal performance.
- Invest strategically to enhance equipment reliability.
What Resources Are Available for Equipment Maintenance Planning?
Numerous resources are available to streamline equipment maintenance planning and enhance overall equipment management. Maintenance management systems provide a platform where businesses can develop a comprehensive maintenance schedule tailored to their specific needs.
These systems not only reduce the likelihood of missed maintenance tasks but also help track historical data, allowing organizations to identify trends that inform future preventive actions, ultimately improving equipment reliability.
Additionally, companies can tap into online platforms and software solutions that promote efficient equipment preventive maintenance.
These technologies often include environmental considerations, ensuring compliance with industry regulations while optimizing performance. By leveraging these resources, teams can take proactive steps to keep machinery in top shape, reducing downtime and boosting overall productivity.
Every piece of equipment has a story worth telling. In the next section, real experiences reveal how simple strategies led to remarkable results.
Why is regular maintenance important for equipment longevity?
Regular maintenance is crucial for equipment longevity as it prevents breakdowns, optimizes performance, and reduces repair costs. Consistent checks ensure all components function effectively, extending the lifespan and reliability of machinery across various operational settings.
What essential tasks should be performed for equipment maintenance?
Regular equipment maintenance includes inspecting machinery, checking fluid levels, cleaning components, tightening bolts, and replacing worn parts. These tasks help ensure optimal performance, extend equipment lifespan, and prevent costly breakdowns.
How can best practices improve equipment lifespan?
Best practices like regular maintenance, proper usage, and timely repairs can significantly enhance equipment lifespan. Implementing these strategies reduces breakdowns, ensures optimal performance, and ultimately saves costs on replacements and repairs over time.
What happens to equipment with poor maintenance?
Poor maintenance of equipment can lead to increased wear and tear, reduced efficiency, unexpected breakdowns, and costly repairs, ultimately shortening its lifespan and impacting overall performance. Regular upkeep is essential for optimal functioning.
Can you share examples of effective equipment maintenance strategies?
Effective equipment maintenance strategies include regular inspections, timely repairs, and implementing a preventative schedule. Utilizing tracking software ensures maintenance tasks are executed, reducing downtime and enhancing operational efficiency for businesses relying on machinery.
Conclusion
Regular maintenance is the cornerstone of ensuring your equipment’s longevity and optimal performance. By staying proactive, you can prevent costly repairs, improve efficiency, and extend the life of your systems.
When it comes to septic system maintenance, trust the experts at Smart Septic Pros for reliable and professional service. Contact us at 678-993-4545 or request a service today! Let us help you keep your septic system running smoothly and efficiently for years to come!